Importance of lacquers in packaging industry
- Lacquers are thin, continuous depositions on foils which form a layer. This film has a specific importance depending on the manner of its use. Lacquers are applied onto both aluminium foils and plastic films.
- Solvent-type lacquers are used predominantly, which is far from optimal considering their effect on the environment. However, the complexity of their chemical composition, in the heat-seal lacquers in particular, is hard to achieve in a water-based system. The water systems are applied as well.
- According to the way they are used, the lacquers are classified as priming lacquers (primers), protective and barrier lacquers and heat-seal lacquers.
- Lacquers applied on food packaging have to comply with the conditions specified by the international hygienic standards applicable for contact with foodstuffs.
Types of lacquers and their application
PRIMING LACQUERS (primers)
They are lacquers designed to fix graphic print on the foil surface, as aluminium foil is difficult to print directly. The lacquer quantities deposited range from 0,8 g/m² to 1,5 g/m². Types based on the cellulose nitrate are the ones used most frequently, and they predominantly form the outer side of the packaging.
BARRIER LACQUERS (protective lacquers)
These lacquers are designed to form a resistant film between the foil and the packaged product that they are in direct contact with. Aluminium is quite unstable both in the acidic and the alkaline environments. It may get corroded or even dissolved due to substances included in the product, which may result in depreciation of the package and contamination of the product packaged with aluminium. Therefore, it is not possible for Aluminium – in terms of both technological and hygienic concerns – to be in direct contact with the packaged product. The lacquers on the inner side of a processed cheese packaging can serve as an application example. The barrier lacquers may also be applied as priming lacquers onto which mainly heat-seal lacquers are subsequently layered. This ensures a completely defect-free layer (so called “brickwork effect“– see below), resistant to such aggressive products as is mayonnaise or mustard for instance. Depositions of these lacquers usually range from 2 g/m² to 4g /m².
HEAT SEAL LACQUERS
The most important, both in terms of use and processed volume, are heat seal lacquers.
HSL
Heat seal lacquers are engineered on the basis of a range of polymers, from acrylates and vinyl chlorides to complex systems of elastomeric copolymers combined with dispersions of polyolefins and other accessory substances.
These lacquers are substances that make it possible to use heat sealing technology, that is sealing aluminium lids or a plastic foil with a plastic cup. These substances are comparatively complex chemical systems which are supposed to meet a whole range of requirements. It must have the ability to seal with different types of plastics, the sealing strength must be neither too high not too low, and the lacquer must have the property to dry up (regarding thicker depositions) during a single passage through the machine, etc. the seal temperature must be optimally set.
This is why they generally get top attention of experts. Heat seal lacquers can be divided into several categories depending on the type of plastic with which they are able to form high-quality seals. The ability to seal with PP, PS, PVC, PE, PVDC, PET, marginally with paper and glass is expected. Heat-seal lacquers are engineered on the basis of a range of polymers, from acrylates and vinyl chlorides to complex systems of elastomeric copolymers combined with dispersions of polyolefins and other accessory substances.
Lacquers for PS, PVC, PET
These lacquers represent a cheap variant of a heat sealable coating, yet there is a cost to be paid – they can only be applied onto PS, PVC and PET materials. They are widely used.
Universal lacquers
They are lacquers that have a capacity to seal (type by type) the whole spectrum of sealing, in particular PP, PS, PE, PVC and PET.
Lacquers for pharmaceutical industry
Al-foils used to seal blister packaging with pills in the pharmaceutical industry make use of special lacquers with enhanced adhesion. They can be used to seal PS and PVC.
Lacquers for processed cheese packaging
These lacquers are specially modified for a low-temperature sealing. It is a foil-to-foil sealing action.
FOIL DEPOSITION
Foil deposition is effected on lacquering machines. As shown in the image, they are rather large devices, sometimes they can even be tens of meters long. There are many types. Usually, it is a two-sided, one-layer deposition effected during a single passage through the machine. To illustrate this process, we are bringing the following chart depicting a high-end-equipped machine with three depositioning sections, plus an optional laminating feature (more layers of foil or paper).

Modes of deposition
SEMIFLEXO PRINTING
It is the single most frequented deposition method for an all-area lacquering of foils. The set-up usually consists of three cylinders. The quantity of lacquer being deposited is regulated through altering the pressure force and the difference in revolutions of the depositing and the wiping cylinders. The lacquer is then transferred onto the foil running between the supporting and the depositing cylinders.
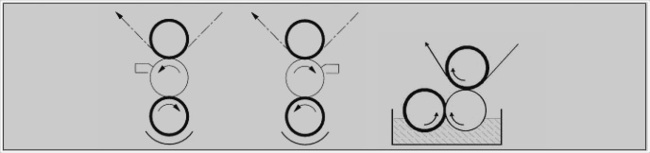
GRAVURE PRINTING
It is a wide-spread techology namely in the sphere of graphic printing, yet, as compared with the semifexo printing, it is used less frequently to deposit lacques onto foils. There is a disadvantage about it: it is impossible in practice to achieve thicker deposition layers in a single step, with the limit value for a commonly used lacquer being around 4g. This is also why the method is utilized to deposit layers with a lower square weight – priming lacquer, for example. The system set-up consists of two cylinders. A gravure printing cylinder retains a certain quantity of lacquer within the raster, and the excess lacquer is wiped away with a blade. The foil passes in between the gravure printing cylinder and the support cylinder, while the raster-retained lacquer is transferred onto the foil.
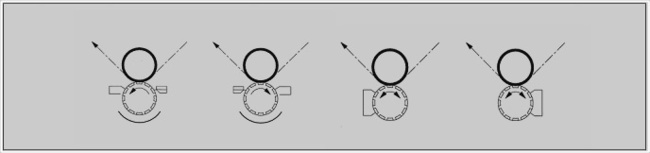
Proven hygienic safety:3
GENERAL
Most lacquer-coated aluminium foils are designed to be used in the food industry as packaging materials. They are largely in the form of lids to seal plastic cups with yoghurt, cream, salads. Packaging for processed cheeses, butter as well. In such cases as are the above, or similar, it is essential to care for the health aspect, for the lacquer-coated foil gets into direct food contact.
LEGISLATION
EU Regulation 1935/2004 covers all food contact materials and articles which are intended to come into contact with food. The Commission regulation (EU) 10/2011 on plastic materials and articles intended to come into contact with food and its amendments incl. 1282/2011, 1183/2012, 202/2014, 174/2015.
Based on the requirements of Commission Regulation (EC) 2023/2006 on good manufacturing practice for materials and articles intended for contact with food, the product is manufactured under the ISO 9001:2009 quality management system.
Quality requirements, demands, parameters and lab testing
GENERAL
Heavy demands are put on lacquers, therefore they are supposed to meet a wide range of parameters. It is the quality and properties of the heat-seal lacquers in particular that have been under a very close scrutiny. As they are being developed, they have to be optimized, as part of the whole system, for good adhesion to surfaces, good rheological characteristics and high solvent volatility, so that the lacquer can dry up well even in thick depositon layers and form a quality film without defects. A possibility to modify the lacquers respective to the differences specific to the individual machines is of the essence. Primers are supposed to provide binding with printing inks. Heat-sealable lacquers are required to create quality joints with a number of materials in parallel. At the same time, they have to resist the chemical effects of the packaged products. Their depositions must not form a block (stick together in rolls), not even at increased storage and transport temperatures. Moreover, all the lacquers are supposed to comply with the aforesaid hygienic conditions, which has to be taken in consideration when choosing the appropriate hygienically suitable input raw materials.
LAB TESTING
The parameters mentioned above need to be verified in the laboratory.
Parameters of the lacquers are monitored on a continuous basis through the check-out procedure by the lacquer maker and the check-in procedure by the customer. Each production batch is inspected through the procedures controlled as part of the introduced system of quality assurance ISO 9001:2001.
Each batch is tested for the basic parameters – the physical properties such as dry content, viscosity and density – prior to the relase from the production facility. In addition, the lacquer´s IR spectrum is measured and compared with the standard.
On the basis of the results, a certificate of quality forming an integral part of each lacquer delivery is issued with each batch.